At My Appliance Guy, we specialize in providing reliable and professional appliance repair services to homeowners across Ohio. Our team of expert technicians is equipped to handle a wide range of appliance issues, and we take pride in offering efficient solutions to restore your appliances to their optimal working condition. Recently, we had the opportunity to perform a washing machine repair job at a residence in Cleveland, Ohio, where the homeowner had been experiencing issues with their washing machine. The appliance was not spinning properly, leaving clothes wet after the wash cycle, and this caused frustration for the homeowner.
In this article, we will walk you through the details of the washing machine repair job, explaining the diagnostic process, repairs made, and how the customer was educated on preventing future issues.
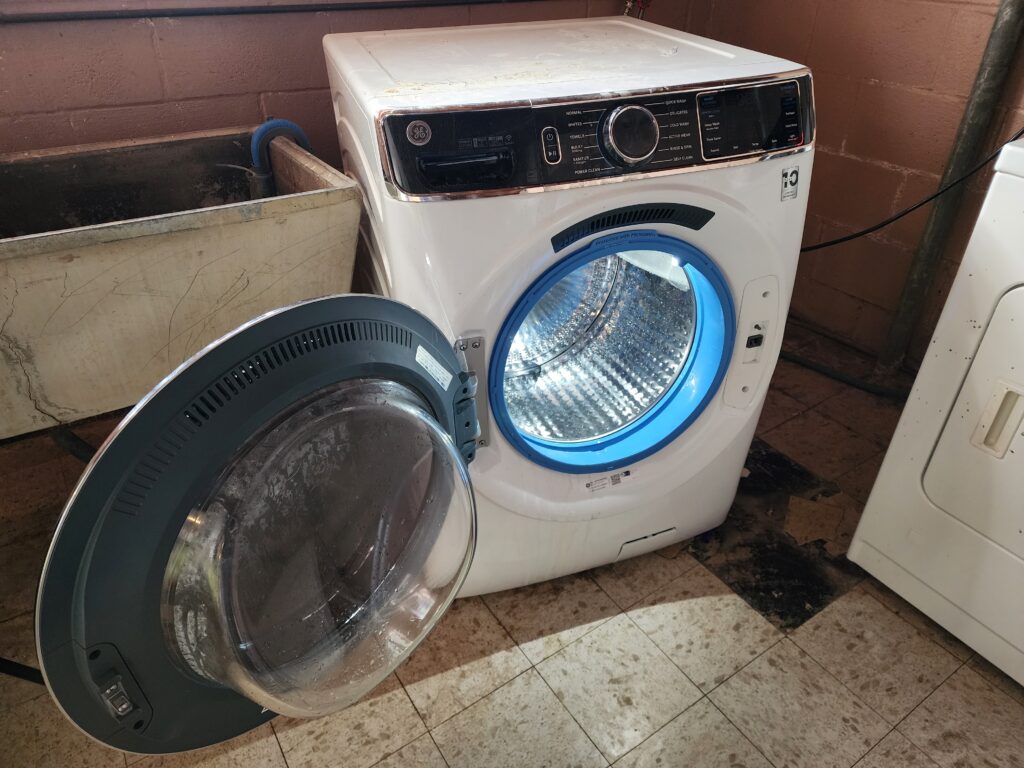
Initial Call and Scheduling the Appointment
The homeowner reached out to My Appliance Guy after encountering problems with their washing machine. They explained that the washer was no longer completing the spin cycle, leaving clothes soaked at the end of each wash. This problem was not only an inconvenience but also an indication of a more significant mechanical issue that needed to be addressed.
The homeowner attempted to troubleshoot the issue themselves, checking the settings and ensuring that the load was not unbalanced, but the problem persisted. Understanding the urgency of the situation, we scheduled an appointment for the next available day, ensuring that the homeowner wouldn’t have to wait long to get the issue fixed.
Arrival at the Cleveland Residence
Our technician arrived at the Cleveland residence on time, ready to assess the problem with the washing machine. Upon greeting the homeowner and receiving more details about the problem, the technician began a thorough inspection of the appliance.
The homeowner mentioned that they had checked the laundry load and ensured it wasn’t too heavy or unbalanced, but despite these precautions, the washer continued to fail to complete the spin cycle. Additionally, they noticed that the washer was making unusual sounds during the cycle, which further pointed to a mechanical issue that needed professional attention.
Diagnostic Process
The technician began by performing a diagnostic test to determine the root cause of the washing machine’s malfunction. The primary symptoms pointed to an issue with the spin cycle, which often involves the drain pump, agitation system, motor, or belts. The technician methodically checked each of these components to rule out potential problems.
1. Inspecting the Drain Pump
One of the first things the technician checked was the drain pump, as improper drainage can cause a washing machine to fail in the spin cycle. The technician started by inspecting the pump and drain hose for blockages or clogs. In some cases, small items like coins, buttons, or lint can get stuck in the drain hose, preventing the washer from draining properly.
Upon further inspection, the technician found that the drain hose was clear of blockages. However, the drain pump itself showed signs of wear and tear, which was causing it to operate inefficiently and fail to drain the water properly from the drum during the spin cycle. The technician determined that the pump needed to be replaced to restore full functionality to the washing machine.
2. Examining the Agitator and Motor
The agitator and motor are essential components of the washing machine, responsible for moving clothes through the wash cycle and powering the drum’s rotation during the spin cycle. The technician checked the agitator to ensure it was working correctly and that the motor was functioning as expected.
The agitator appeared to be working, but the technician noticed that the motor was struggling to turn the drum with full power. This indicated that there could be an issue with the motor’s drive belt, which connects the motor to the drum and powers the spin cycle. The technician checked the motor and belt system to confirm that the motor itself was not damaged, but the belt was indeed worn down and slipping.
3. Inspecting the Belt and Pulley System
The belt and pulley system is a critical component in many washing machines, as it helps drive the drum’s rotation during the spin cycle. The technician removed the front panel of the washing machine to inspect the belt and pulley system. Upon inspection, it was clear that the drive belt had stretched and was no longer providing the necessary tension to power the drum. This caused the washing machine to fail during the spin cycle, as the drum was not rotating with sufficient force to wring out the clothes.
The technician carefully removed the old drive belt and replaced it with a new one. After installing the new belt, the technician ensured that the tension was just right, as too much slack could cause future issues, while too much tightness could strain the motor.
Repairing the Washing Machine
With the necessary parts identified, the technician replaced the drain pump, drive belt, and ensured that the motor and agitator were working as expected. Once the new components were installed, the technician reassembled the washing machine and performed a series of tests to verify that the repairs were successful.
1. Testing the Spin Cycle
The technician ran several spin cycles to check for any remaining issues. After replacing the parts and ensuring the system was running smoothly, the washing machine successfully completed each cycle without any errors. The drum spun efficiently, and the clothes were wrung out thoroughly at the end of the cycle. The washing machine was now back to its normal operating condition.
2. Ensuring Proper Drainage
With the new drain pump installed, the technician also ran a test to ensure that the water was draining properly from the washer. The pump performed well, and the washer drained all water during the cycle, leaving the drum ready for the spin cycle without any water retention.
Customer Education and Maintenance Tips
Once the washing machine repair was completed and the appliance was functioning perfectly, the technician took time to educate the homeowner on how to maintain their washing machine to avoid similar issues in the future. The technician recommended the following maintenance tips:
- Check the drain filter regularly: The homeowner was advised to clean the drain filter periodically to prevent debris and lint from building up and causing blockages in the pump.
- Avoid overloading the machine: Overloading the washer can cause strain on the motor and belts, leading to performance issues. The technician recommended loading the washer according to the manufacturer’s specifications for optimal performance.
- Inspect the hose for leaks: Leaky hoses can cause water to pool at the bottom of the machine or in the laundry area, potentially leading to more significant damage. The homeowner was advised to check the hoses periodically for signs of wear.
- Run maintenance cycles: The technician suggested running a maintenance cycle with washing machine cleaner every few months to keep the washer in top shape and remove any accumulated soap scum or mold.
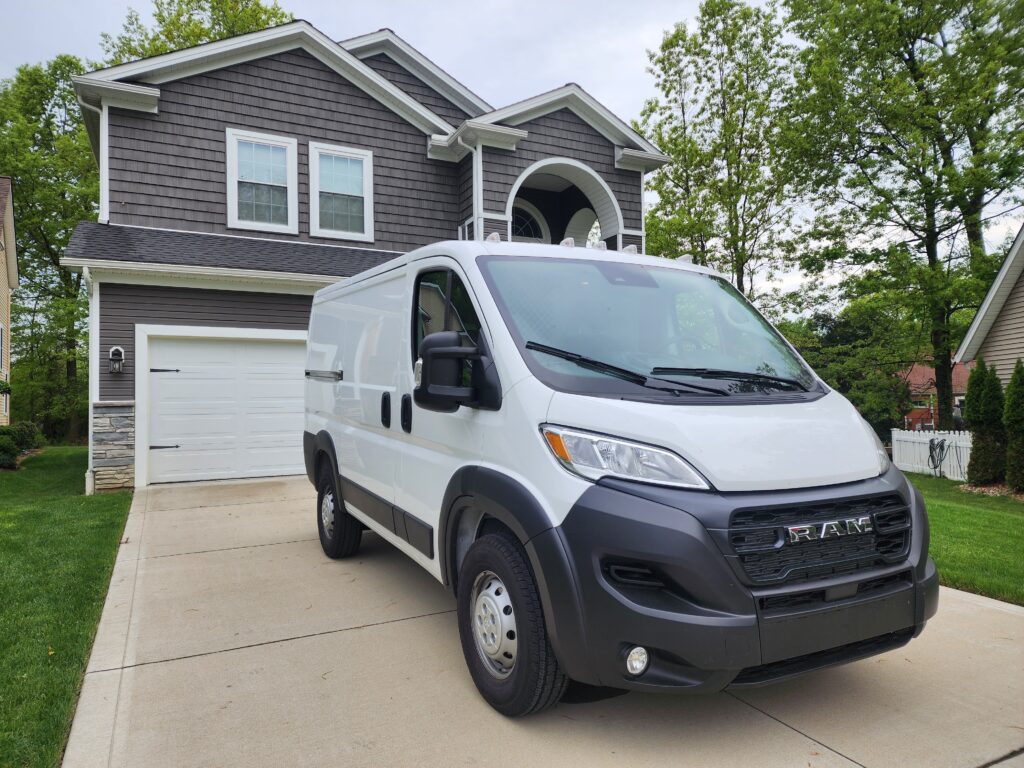
Conclusion
The washing machine repair job in Cleveland, Ohio was a success, thanks to the expert service provided by My Appliance Guy. By diagnosing the issues with the drain pump, drive belt, and motor, our technician was able to restore the washer to full functionality. The homeowner was pleased to have their washing machine back in action and appreciated the technician’s professionalism and clear explanations of the repairs.
At My Appliance Guy, we are committed to providing prompt, efficient, and professional appliance repair services to homeowners in Cleveland, Ohio, and surrounding areas. Whether you’re dealing with a washing machine issue or need help with another appliance, our skilled technicians are ready to help. Contact us today to schedule a service and get your appliances working like new again.